In the world of modern technology, 3D printing has emerged as a ground-breaking innovation that has revolutionized manufacturing and design processes. This technology, also known as additive manufacturing, allows for the creation of three-dimensional objects by layering materials based on digital models. From creating prototypes and custom parts to manufacturing complex structures, 3D printing offers endless possibilities.
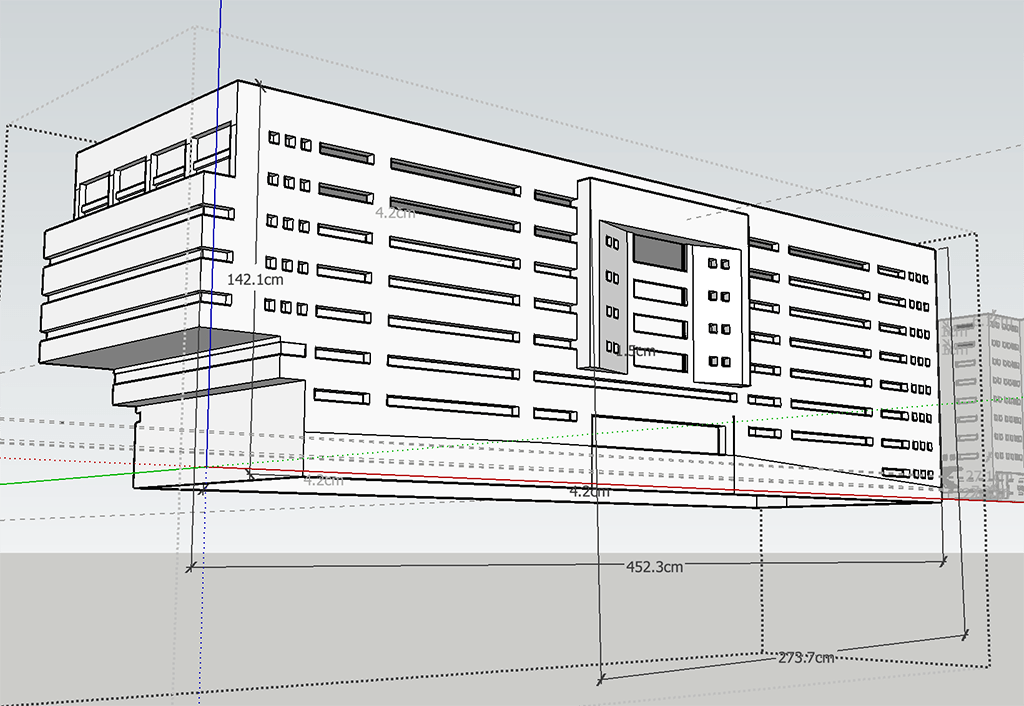
Understanding 3D Printing
3D printing is the process of creating a physical object from a digital model by adding material layer by layer. Unlike traditional manufacturing methods, which often involve subtracting material from a larger block, 3D printing builds objects from the ground up. This allows for the creation of complex and intricate designs that would be difficult or impossible to achieve with conventional techniques.
The Printing Process
The process can be broken down into several key steps:
1. Designing the Model
The first step is creating a digital model of the object to be printed. This can be done using computer-aided design (CAD) software or by scanning an existing object to create a digital replica. The digital model is then converted into a format that the printer can read, usually an STL (stereolithography) file.
2. Preparing the Printer
Once the digital model is ready, the next step is to prepare the 3D printer. This involves setting up the printer, loading the appropriate material, and configuring the printer settings based on the specifications of the model. The settings may include parameters such as layer height, print speed, and temperature.
3. Printing the Object
With the printer prepared, the 3D printing process begins. The printer reads the digital model file and starts to build the object layer by layer. Depending on the type of printer and the complexity of the design, this process can take anywhere from a few minutes to several hours or even days.
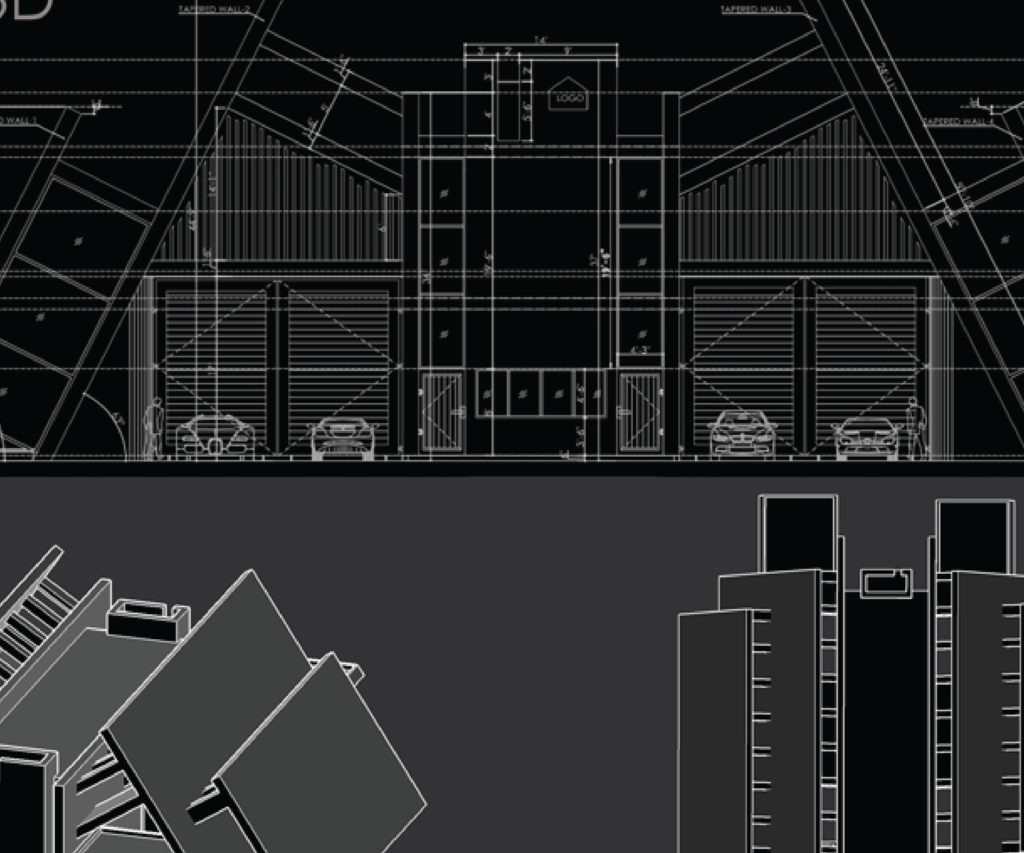
4. Post-Processing
After it is complete, the object may require some post-processing. This can include removing any support structures used during printing, sanding rough edges, or applying finishes such as painting or coating. Post-processing helps to improve the appearance and functionality of the final product.
Types of 3D Printing Technologies
There are several different these technologies, each with its own unique methods and applications. Here are some of the most common types:
1. Fused Deposition Modeling (FDM)
Fused Deposition Modeling (FDM) is one of the most widely used 3D printing technologies. It works by extruding a thermoplastic filament through a heated nozzle, which melts the material and deposits it layer by layer to build the object. FDM is popular for its affordability and ease of use, making it ideal for hobbyists and small businesses.
2. Stereolithography (SLA)
Stereolithography (SLA) uses a laser to cure liquid resin into solid layers. The laser traces the design of each layer onto the surface of the resin, causing it to harden. SLA is known for its high resolution and ability to produce detailed and intricate objects, making it suitable for applications in industries such as dentistry and jewelry.
3. Selective Laser Sintering (SLS)
Selective Laser Sintering (SLS) uses a laser to fuse powdered material into solid layers. The laser selectively sinters the powder, binding the particles together to form each layer. SLS is capable of producing strong and durable objects from a variety of materials, including plastics, metals, and ceramics. This makes it a popular choice for industrial applications.
4. Digital Light Processing (DLP)
Digital Light Processing (DLP) is similar to SLA but uses a digital light projector to cure the resin instead of a laser. This allows for faster printing speeds and higher resolutions. DLP is commonly used for producing small, detailed parts and is favored in industries such as healthcare and electronics.
5. Multi Jet Fusion (MJF)
Multi Jet Fusion (MJF) uses a combination of inkjet printing and powder bed fusion to create objects. A layer of powder is spread across the build platform, and inkjet nozzles deposit fusing agents onto the powder, which are then fused together using heat. MJF is known for its speed and ability to produce complex geometries with fine details.
Applications
3D printing has a wide range of applications across various industries. Here are some of the most notable:
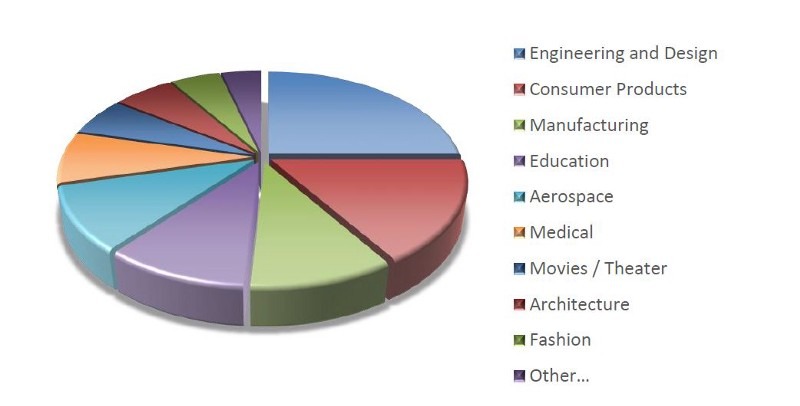
1. Prototyping
3D printing is extensively used for prototyping, allowing designers and engineers to quickly create and test their ideas. This reduces the time and cost associated with traditional prototyping methods.
2. Healthcare
In healthcare, 3D printing is used to create custom prosthetics, dental implants, and even bioprinted organs and tissues. The ability to produce patient-specific medical devices has revolutionized personalized medicine.
3. Aerospace and Automotive
The aerospace and automotive industries use 3D printing to produce lightweight and complex parts that are not feasible with traditional manufacturing methods. This helps to improve performance and reduce costs.
4. Education
3D printing is becoming increasingly popular in educational settings, providing students with hands-on experience in design and engineering. Schools and universities use 3D printers to teach concepts in STEM (science, technology, engineering, and mathematics) fields.
5. Art and Design
Artists and designers use 3D printing to create unique and intricate pieces that push the boundaries of traditional art forms. The technology allows for the creation of complex shapes and structures that would be difficult to achieve by hand.
6. Construction
In the construction industry, 3D printing is used to create building components and even entire structures. This has the potential to reduce construction time and costs while allowing for innovative architectural designs.
Future Prospects
The future of 3D printing is bright, with ongoing advancements in technology and materials expanding its potential applications. Here are some exciting developments to watch for:
1. Advancements in Materials
Researchers are continually developing new materials for 3D printing, including biodegradable plastics, advanced composites, and even edible materials. These innovations will open up new possibilities for various industries.
2. Increased Speed and Efficiency
As 3D printing technology continues to evolve, we can expect faster and more efficient printers. This will make 3D printing more accessible and practical for large-scale production.
3. Integration with Other Technologies
The integration of 3D printing with other technologies, such as artificial intelligence and the Internet of Things (IoT), will enhance its capabilities. For example, AI can optimize designs for 3D printing, while IoT can enable real-time monitoring and control of 3D printers.
4. Expansion into New Industries
As 3D printing becomes more advanced, it will continue to expand into new industries and applications. This includes areas such as fashion, food, and pharmaceuticals, where 3D printing can offer unique advantages.
Conclusion
3D printing is a transformative technology that has the potential to revolutionize the way we design, create, and interact with objects. From prototyping and healthcare to aerospace and education, its applications are vast and varied. As technology continues to advance, 3D printing will become an even more integral part of our lives, driving innovation and enabling new possibilities.